Technology
General Process Description
Pulp & Paper Manufacturing Agro-Pulping
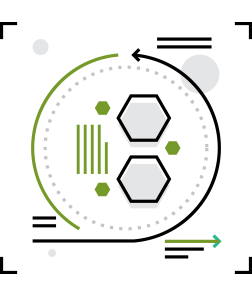
Agro-Pulping
The agro-wastes such as bagasse etc. are received from nearby area. The raw material contains pith, dust and fins etc. which are considered non-process elements. These are removed by dry-depithing or dry de-dusting before being fed into washing section. The pith so obtained from the dry depithing are fired in boiler as it has a good calorific value in washing section, The raw material is passed through pulper/ drum washer. The raw material is washed only with the available backwater from the process sections. Due to vigorous Agitation in the pulper, the other non-process elements are also removed. Some part of free water is carried along with the raw material which is then fed into aqua-separator. The aqua-separator helps in removing the excess water from raw material .
The depithed/ deducted & washed material is then squeezed into screw press. The water so obtained from aqua—separator &screw press is collected & screened in B-2 thickener for reuse again in pulper. The raw material from screw press is carried by conveyors on to metering screw into the plug feeder which makes a compact plug to feed raw material to digester where steam & caustic are added. The digester tubes are provided with timer screw so that residence time of material can be controlled. After cooking, the pulp is passed through cold blow discharge into blow tank In cold blow discharge, the cool liquor is passed to dilute the pulp & to reduce the temperature.
The pulp from blow tank is pumped into vibrating screens to remove unwanted & uncooked material & recycled bock for recovery of valuable fibers from it. The low consistency pulp (about l.5% cy) contains black liquor and fiber. The brown stock pulp or the unbleached pulp is then fed into 3-sloge brown stock washers where the pulp is washed in counter-current sequence with the foul condensate from recovery section. The liquor obtained from the first stage is pumped to recovery section for recovery of valuable caustic from black liquor. The process details of recover section ore given separately.
After brown stock washing, the pulp is again cleaned in centricleaners and slotted screens so that maximum non-process elements can be removed. The clean brown pulp is then subject To thickening in decker—Thickener to increase the consistency of pulp.
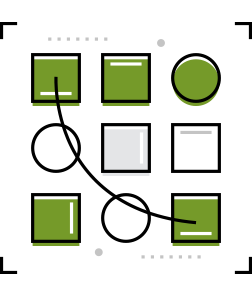
Chlorine Di-Oxide Preparation
The sodium chlorate (NaCLO3) is imported in safe HDPE bags. The sodium chlorate is allowed to react in two—stage reactor system with hydrogen peroxide in strong sulphuric acid solution to produce CLO2. The reaction by-products are oxygen & waste acid containing sodium bi-sulphate. The main advantages of this system are lower capital cost, chlorine free product, high yield of CLO2, reduced pollution load on mill effluent. .

Environment- Friendly Bleaching Process
CLO2 - Oxidative - CLO2 (D0 — OX — D1 STCIQGS) D0 Stage - Bleaching with Chlorine di-oxide OX - Oxidative bleaching. D1 Stage — Bleaching with chlorine di-oxide The unbleached pulp is subject to bleaching by Chlorine di-oxide - Oxidative bleaching with oxybleach — Chlorine Di-oxide (D0- OX- D1) sequence. The sequence is adopted so that the AOX levels are retained within the permissible limits. The chlorine (CLO2) is added in first stage to loosen the Lignin from the cellulose fiber. Oxidative bleaching is used in intermediate stage. The chlorine di-oxide is added in the 3rd stage of bleaching to achieve the desired brightness level of 85-86% ISO. The main advantages of adopting this bleaching sequence are — .
- Reduction in BOD, COD & AOX in bleaching plant effluent by 30-35%. /li>
- The oxidative bleaching selectivity removes residual lignin from the fiber and facilitates bleaching with less pollution load.
- Gain in concentration of black liquor resulting better run ability of chemical recovery plant.
- Improvement in pulp quality, i.e., gain in brightness, viscosity & strength properties.

Wood Pulping/ Broke Pulping -
The imported soft wood pulp and broke obtained from manufactured paper is subject to mixing & slushing with water in separate pulpers. The wood pulp/ broke street is then cleaned in vibrating screen to remove unwanted material contained in them. Then the pulp is passed through high density cleaners to remove dirt particles. The cleaned pulp is then mixed with the bleached agro-pulp in certain required proportion. .
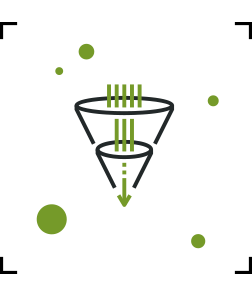
Filler (GCC)
GCC is added to pulp which works as filler and improves properties of paper. GCC is available in powder form and it is mixed with water and the solution so obtained is processed through vibrating screens to remove the undesired particles from it. .
Stock Preparation
The agro-pulp/ broke pulp are mixed in certain proportion in the mixing chest. Other chemicals like retention aid, optical brightening agents, dyes, GCC and sizing chemicals are added in blending chest in the pulp to improve the pulp optical & physical properties. The final pulp is then ready for paper manufacturing at paper machine. .
Paper Machine
The pulp is then pumped into machine chest and then to approach flow system containing of fan pump, centricleaner and pressure screen. The final clean pulp goes to paper machine head box which spreads the fiber uniformly across the synthetic forming fabric. From head box, the fiber passed over fourdrinier table where approx. 50% of total water is removed from the pulp. .
The pulp now is in sheet form and contains some amount of free water. The sheet is then pressed into series of presses to remove the free water from it. The paper sheet is then passed into series of steam heated driers so that the inherent moisture from paper fiber is removed. .
Sizing
Before fully drying the paper, it is subjected to sizing. The paper web is rewetted with a starch based solution. The process is called surface sizing. The size — starch solutions are applied to the paper web by means of mechanical presses (size press). Together with surface sizing agent the surface starches impart additional strength to the paper web and additionally provide water hold out or "size" for superior printing properties. The sized paper has improved smoothness, stiffness, whiteness and strength and thus improves printing characteristics. .
Calendaring & Reeling
Finally, the sized paper is calendared to improve the smoothness of paper & reeled onto spools over pope reel. .
Finishing
The paper spool roll is taken on rewinder where the paper is rewinded into certain specific sizes as per the demand from the market. The paper demand of sheets is met through three sheet cutters where paper is cut into sheet form as per the order. These reels or sheets of bundle are packed & weighed before final dispatch to the respective customers.
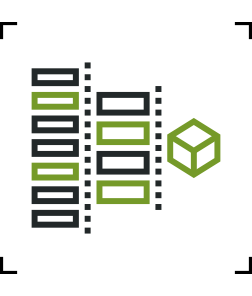
Conclusion
The use of environment-friendly techniques and eco-friendly products in pulp & paper manufacturing gives a whole new dimension to the industry. Today, as the population increases at rapid rate, the demand for paper increases too. To feed this demand, the forest based raw materials are becoming scarce. So the industry & research institutions are searching new products for preparation of Pulp & paper. Bindals Papers Mills Limited is one such industry that is using eco-friendly technology to manufacture the paper and has earned a good name in the market by producing quality paper using the agro-based raw materials. In present scenario Bindals has adopted a big effort to save earth and our rivers by adoption of ZLD technology in mill. Bindals is first mill globally to achieve such practices among agro based integrated pulp & paper mill. The management is eager to introduce new concepts in development of new products by using safe & sound technologies that also pose no danger to the environment & natural resources by keeping itself sustained in the market. Use of enzymes is one such approach in which the industry is keen to venture further to reduce the production cost and to develop clean & green products. .